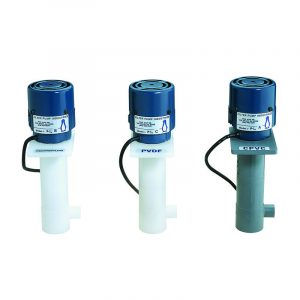
We’re stocking more and more pumps and parts such as these Penguin Series P vertical sealless pumps.
Supply chain disruptions may no longer grab the headlines on the nightly news but for manufacturers depending on every minute of production to stay afloat, shortages and lead time delays continue to wreak havoc on a daily basis. It’s devastating when a common wear part fails, a production line shuts down, and the purchasing manager finds out the replacement part is unavailable or back ordered with a three-month lead time. Unfortunately, it’s tough to know exactly what products and parts are in short supply until it is too late.
We are seeing major delays in electronics for heaters, controllers, heating components, and PVDF materials for both vertical sealless pumps and centrifugal magnetically driven pumps. How long is a major delay? With heaters and controllers, the lead times can be upwards of 16-20 weeks. Try managing a production shutdown for five months.
We have increased our stock of Penguin vertical pump and motor assemblies, and thermostats for Process Technology controllers, and we’ve assembled and added more Wilden pump repair kits, among other purchases.
We recommend you do the same. Stock backups of any part or product that can shut your production down if it becomes unavailable. Start with getting repair kits for all of your AODD pumps, get extra motors and impellers for any vertical pumps, wet end kits for magnetically driven pumps, and/or complete pump units as the budget allows. Pump manufacturers often discontinue models and getting your hands on exactly the right replacement in the event of a failure is proving to be quite a challenge for many frustrated plant managers.
We also recommend avoiding pump and process equipment failures in the first place by performing preventative maintenance. In metal plating, for example, the material that strips off the cleaned parts can build up on the heaters and cause premature failures. But this is entirely avoidable with routine cleaning. Similarly, it doesn’t take long to check the diaphragms of an air operated double diaphragm pump to make sure there’s no leakage. Catch any leakage before a failure and it’s a relatively easy kit replacement. But waiting until a failure can invite a much bigger disaster.
We help our customers avoid disasters and when a customer calls us in a bind, scrambling for a rush part or product, we try to drop everything and ship out the exact part or product immediately. Of course, even we can’t stock every pump, heater, and component in our warehouse. But we can often find the solution within our extensive network of manufacturers. Or, we can find an alternative solution that is more readily available.
Times are crazy – even if we’re not hearing about it at the top of the news every day. Please know that we are constantly working to source and stock the pumps and parts you need to keep your business running. We’re a family-owned, American distributor with real people who understand the pumps and other equipment offered on the Website. We’re happy to help you get exactly what’s needed and can help you figure the tags, model numbers, and other information even if it’s no longer legible.